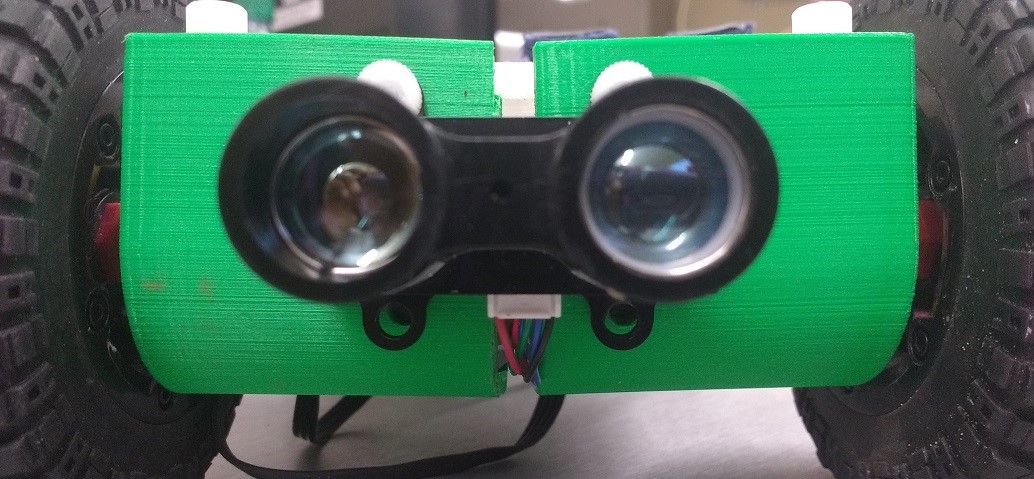
NASA Requirements
The following requirements for the rover were set in the 2018 NASA Student Launch Handbook
- Teams will design a custom rover that will deploy from the internal structure of the launch vehicle.
- At landing, the team will remotely activate a trigger to deploy the rover from the rocket.
- After deployment, the rover will autonomously move at least 5 ft. (in any direction) from the launch vehicle.
- Once the rover has reached its final destination, it will deploy a set of foldable solar cell panels.